Published in Electrosonic's Promag Archive. Click here to read more.
The days when radio presenters were only heard and not seen are long gone. Radio stations started utilising webcams in studio, to stream live video feeds to websites. A number of radio shows started televising presenters and guests in action. This was the start of a new phenomenon that elevated radio broadcasting to a whole new level: a level that rises higher with every sunrise as new technological innovations see the light.
Digital signage is another key part of today's video technology offering. Video walls are a hot topic currently, and if they are used in concert with other new technologies they produce an extremely functional and impressive outcome. When one combines the above design elements with a GALAXY Video Wall processor and NEC professional displays the result is a breath-taking solution that satisfies even the hungriest technological appetite.
Primedia Broadcasting, a leader in their field with cutting-edge stations such as Talk Radio 702 and 947 Highveld Stereo, decided to do a simple makeover: upgrade their existing studio equipment from analogue to digital, slap on a fresh coat of paint, and replace a chair or two. They kicked off with routine design meetings, but as the team brainstormed through the various options and available solutions, the idea of a simple make-over evolved into a magnificent ‘Complete New Studio’ project with video and digital signage becoming core focus points. Grant Vick, project manager for Primedia explained their motivation: “Initially we only wanted individual screens in each of the new studios in order to display content from social media websites such as Facebook and Twitter, as well as live broadcasting from sport matches and breaking news as it happened. We also wanted to utilise the same screens to display different branding inside the studios at different times instead of the conventional fixed printed branding.”
The Primedia project team then approached Spectrum Visual Networks, a digital media company that has been trading for 12 years. Discussions were initiated by putting the above ideas on the table and Primedia emphasizing the importance of video displays within the new studio design.
Primedia operates in the ultra-competitive ‘around the-clock’ broadcasting climate, so a successful solution had to be designed with products that offer 24/7 operation and warrantees. This was a piece of cake for Grant Neill, business development manager for Spectrum Visual Networks, who has ample experience in video technology. Grant did his homework and presented a unique digital media solution second to none. This consisted of multiple NEC ultra-narrow-bezel displays, grouped in adjacent clusters, to form a series of 2x2 and 2x1 video walls. The content for these walls was to be driven by a single GALAXY video wall processor per floor. This solution did not only successfully introduce the video element to the studio project, but also opened up other flexible possibilities. These include unlimited branding options during different radio shows and interviews, computer graphics and multiple live television feeds on display at any time.
The Primedia team loved the idea and together with Grant, they paid a visit to the Electrosonic SA showroom for a demonstration and a first-hand experience of the NEC X463UN direct backlit LED displays. The WOW factor was created and they were blown away. The installation, like many others, did not have a smooth execution and presented a hierarchy of challenges. LCD screens inside the studios had to be mounted flush with the acoustic panels and therefore left limited space for mounting hardware. Instead of using equipment pertaining to video wall installations, standard flat brackets had to be used. The latter however, made the panel alignment much more difficult.
Another unforeseen challenge was the noise level of the GALAXY processor which was designed to be inside the call-screen room, sandwiched between the two studios. The call-screen room, which is used for recording phone calls, has to be extremely quiet and even though the GALAXY was configured accordingly, it still didn’t meet the minimum required decibel levels. The only solution was to move the GALAXY processor to a downstairs server room; in theory a rock-solid plan which worked, but was trailed by more complications. The biggest being the distance between the displays and the video wall processor. It was simply too far for aidless HD distribution. One also had to comply with the prescribed – and already over-populated - cable routes into the studios (in studio construction acoustic treatment, ambient noise blanking and magnetic interference are top priorities and therefore don’t allow new cable routes to be made). The distance to be covered was just shy of 90 meters and in order to display full HD signals (1920x1080, 60Hz), Kramer HDMI transmitters and receivers were introduced.
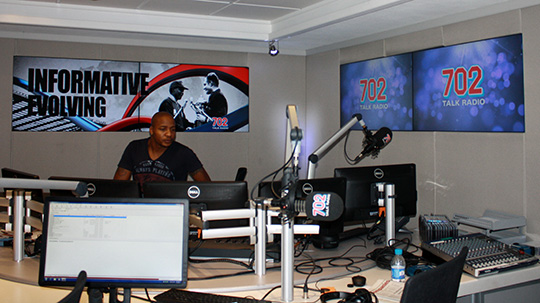
Kramer’s DigiKat7 shielded twisted pair cable which was specifically designed for this type of application, completed the link. With the GALAXY processor now miles away and all the Kramer distribution equipment in place, the Full HD signals reached the displays problem-free and the images were literally ‘spotless’.
On the software side of the GALAXY we faced two challenges. In the GALAXY Wall Control software layout, the entire wall was displayed as one canvas instead of the multiple smaller walls in the studios. This was easily overcome and the programmer simply had to keep his focus while designing the layouts. Another challenge was the layout selection from individual studios. Each studio has five or six different layout options and because it is driven by a single controller, we had to carefully design layouts to accommodate both studios. This was also not too big an issue and we created a lookup-table of 30 layout combinations in order for each studio to operate independently from the other and still have maximum flexibility.
Graphical user-friendly control is maximised by a single Crestron CP3 processor and three TSW750 in-wall touch panels, one in each studio and the call-screen room. The Crestron system is also used to control the source equipment as well as various lighting zones in multiple areas.
All the elements came together well, composing a stunning final product. "We are very impressed by the final result and the vast functionality offered by the new digital signage system. By using technologies such as these, our studios will always have the edge", said Ryan Till, Chief Operating Officer for Primedia Broadcasting. Grant Neill from Spectrum Visual Networks added: “It was a challenging request, but I am very proud to have been a part of such a unique and successful project”.
At Electrosonic SA we are all smiles. Once again a flagship solution came together by using quality products. It’s the reason why we are in this industry and we strive to meet the future with this same vision. We thank all the stakeholders for giving us this opportunity and for their investment in our arsenal of quality products. The final result speaks for itself.